Reynolds built its own UHF RFID-based system to track its approximately 60,000 reusable crates as they are packed, then shipped to and returned from customers; the company is now examining other ways in which the technology could help track product shipments or forklift transit efficiency at its distribution center.
Aug 03, 2018—
When fresh food distributor Reynolds Catering Supplies transitioned out of using disposable cardboard boxes for delivery to its restaurants, cafés and hospital customers, it introduced a more durable, reusable and higher-value plastic crate, also known as a tote. But that transition created a new challenge for the company, which delivers nearly 1 million crates of food across the United Kingdom each year: namely, managing those totes and ensuring that they are returned.
The company decided to create a solution employing RFID technology, and used its own IT team to create software that can be integrated with its own enterprise resource planning (ERP) system. It acquired fixed RFID readers from Impinj and worked with Avery Dennison to identify the most durable and effective tag for that purpose.
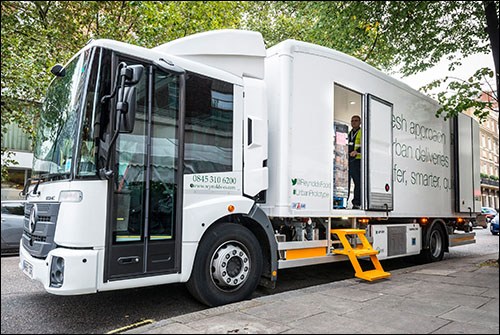
The result is a system that automatically identifies when each crate is packed according to a specific order, as well as when it is shipped and when it returns. Armed with that data, the company can now identify where its totes end up delayed or missing, and thus address the problem. Since the system was taken live with some of its customers one year ago, says Richard Calder, Reynolds’ IT director, it has saved the firm approximately £150,000 ($197,000) in the cost of replacement totes. “We are confident when the plastic totes are fully rolled out to [all] clients that the annual savings will be in excess of £350,000,” he says. In addition, the technology could be used in the future to track food orders.
Source: Fresh Food Provider Sees £150,000 Savings With RFID – 2018-08-03 – Page 1 – RFID Journal